When it comes to manufacturing a product, choosing the right type of material is crucial. This involves carefully considering the intended use of the product, the cost of production, and regulatory requirements that need to be met. With numerous options available it can be challenging to determine the most appropriate choice.
Silicone and thermoplastic elastomers (TPEs) are two popular options among the different materials available in the healthcare, pet, and consumer industries. Both materials have unique qualities that make them suitable for various applications. To determine which material is best suited for your product, let's compare the properties and features of silicone and TPEs.
Silicones
Silicone is a popular material used for manufacturing products. It has a smooth, rubber-like texture, is naturally hypoallergenic, odorless, and is highly durable, maintaining its properties even after prolonged repetitive usage. Due to its food-safe properties and ability to meet FDA and USP Class VI requirements, it’s a popular material for use in food and beverage applications and medical molding products. Silicone is available in a range of durometers on the Shore A scale, with a softer range of 3 to 80 and a lower "sweet spot" of 50. It bonds strongly with other silicones when overmolding and has low molding pressures. Silicone may contain ingredients that are designed to impart specific properties, such as pigments for custom colors and additives that control cure speeds. To promote product safety, designers can specify food-grade or medical-grade silicones that meet standards from the U.S. Food and Drug Administration (FDA) and the U.S. Pharmacopeia (USP).
Thermoplastic Elastomers (TPEs)
Thermoplastic elastomers (TPEs) are another material used for manufacturing a wide range of products. TPEs are similar to silicones in many ways, including low extractable levels, easy-to-clean surfaces, and flexibility. TPEs can be melted and reprocessed multiple times, making them a more sustainable choice. They also offer the advantage of being easier to work with in overmolding applications, as they bond well with most common plastics. TPEs are available in a wider range of hardness levels but may lose their properties when subjected to repetitive usage, harsh conditions, and chemicals.
Silicone vs TPEs: Considerations for Your Products
- Durability: Silicone is highly durable and maintains its properties even after prolonged and repetitive use in various environments. It is inert to most chemicals and can function reliably in temperatures ranging from -100F to 450F. On the other hand, TPEs can permanently deform and/or lose their properties when exposed to chemicals, wide temperature ranges, and repetitive usage.
- Durometers: Both materials are available in a range of durometers on the Shore A scale. However, silicones come in a softer range of 3 to 80 with a lower "sweet spot" at 50 on the Shore A scale. TPEs have a higher range of 20 to 95 on the Shore A scale and tend to be harder than silicone. As an example, the difference between the ideal hardness for silicone vs TPEs are roughly the difference in hardness between a baby bottle nipple vs tire tread.
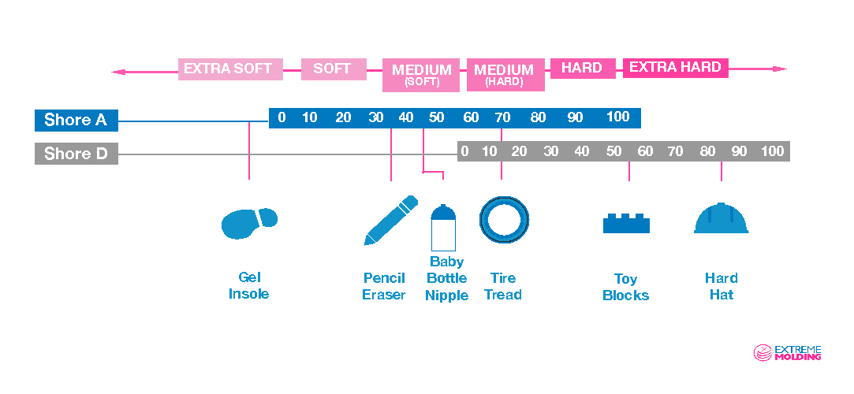
- Food Safety: When making their products, designers can select food-grade or medical-grade silicones that meet standards from the U.S. Food and Drug Administration (FDA) and the U.S. Pharmacopeia (USP). This makes silicone a preferred material for anything that would be going in someone’s mouth.
- Levels of Extractables: Both materials have low levels of extractables, meaning they do not release substances that can migrate to the product's surface after exposure to high temperatures during manufacturing or use.
- Bonding Compatibility: TPEs bond not just to other TPEs, but to most common plastics, such as Polypropylene and ABS. By contrast, silicones only bond readily to other silicones.
- Re-molding: Once molding is complete, silicones cannot be melted down and reprocessed. In contrast, TPEs can be ground down into pellets, re-melted, and then re-molded multiple times.
- Overmolding: TPEs are more suitable for overmolding with a plastic substrate than silicones. However, silicones bond strongly when overmolding with other silicones.
- Customization: Silicones and TPEs can both be custom compounded and engineered to impact specific properties, such as pigments for custom colors and additives that affect cure speeds. Silicones often require custom compounding at the raw material manufacturer, while TPEs can more simply be modified by simply adding an additive in pellet form just before the molding process.
- Resistance to Sunlight and UV Rays: While silicones naturally resist sunlight, TPEs offer moderate resistance to UV rays and require an additive to improve UV resistance.
Choosing Between TPE vs Silicone: Key Factors for Your Decision
When choosing between silicone and TPEs, it is important to consider your specific needs. Both materials have unique advantages and drawbacks. Here's a simple guideline to help you choose:
- Use Silicone when durability, heat resistance, and safety for medical or food applications are priorities. Silicone excels in extreme environments, making it ideal for products that need to withstand high temperatures, chemicals, or repeated use, such as medical devices, kitchenware, or outdoor equipment.
- Use TPE if cost, ease of processing, or recyclability is more important. TPEs are great for products requiring flexibility in manufacturing, like those needing overmolding with common plastics or environmentally conscious applications where reusability is key, such as consumer electronics or packaging.
Ultimately, we recommend seeking assistance from suppliers and molders to make an informed decision, as the material selected can significantly impact your product line. Contact us to discuss your products and ask any silicone vs TPEs questions that you may have.