Designers of baby care products need safe, clean materials with the right performance properties and processing capabilities. When it comes to selecting the right material for your baby product, the choice between silicone and thermoplastic elastomers (TPEs) becomes essential. Both materials have distinct attributes, and making an informed decision ensures that your product not only meets the highest safety standards but also provides the desired comfort, durability, and functionality for both babies and parents alike.
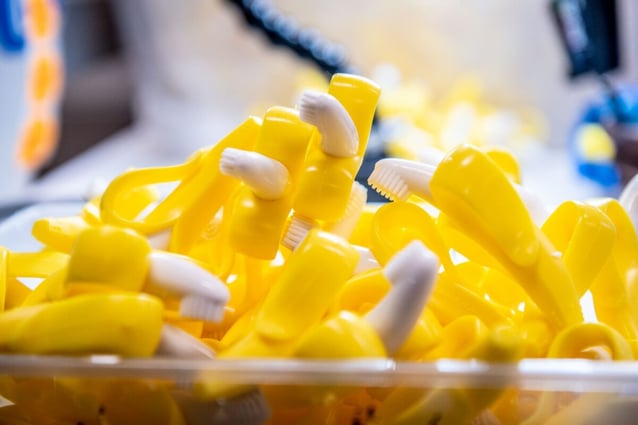
When should you choose silicone for baby products?
Silicones, a group of synthetic elastomers, are a great option when you are looking to produce a product that's durable and long-lasting. It can be used in various baby care products such as pacifiers, baby bottle nipples, feeding sets, sippy tops, seals, and bottle liners. Silicones that meet FDA and USP Class VI requirements for biocompatibility are widely trusted because these materials won’t produce a toxic or immunological response when exposed to the body or bodily fluids. That’s why manufacturing silicone teethers or other silicone-based products are a good choice when trying to meet safety concerns.
When should you choose TPEs for baby products?
Because silicones can cost more than other elastomers, some designers of infant care products may consider using thermoplastic elastomers (TPEs) instead. Like silicones, TPEs can have very low levels of extractables, compounds that migrate from the surface of an infant care product. That’s important because it’s safe to assume that anything babies touch will end up in their mouths. Rattles, bath toys, and baby grip toys aren’t supposed to be used like teething rings, but infants have their own ideas. Additionally, if reprocessing is important, you may want to consider creating a TPE baby product prototype.
Which material properties are important to consider for your baby care product?
At room temperature, silicones and TPEs can have very similar properties. They’re also similar in appearance. At elevated temperatures, however, silicones exhibit better resistance to chemicals and abrasion. Heat and chemicals aren’t usually associated with baby care products, but consumers boil baby bottles, pacifiers, and sippy tops – or treat them with steam or chemical sterilization. Baby spoons, plates, and cups that are put in the dishwater are subjected to abrasive detergents and hot water.
When subjected to heat or repetitive usage (such as squeezing), TPEs can deform permanently. In other words, products made of these materials may not return to their original shape when heat is removed or usage stops. By contrast, silicones have superior memory and elasticity at a wide range of temperatures – including heat. Plus, silicones maintain their material properties over a virtually unlimited amount of repetitive usage.
Silicones and TPEs also differ in terms of available durometers, or hardness. Lower-durometer elastomers are softer and more compressible. Higher-durometer elastomers are harder and more impact resistant. Silicones have a typical range of 3 to 80 durometer on the Shore A scale. TPEs have a typical range of 20 to 95 (Shore A). As the durometer relates to performance, silicones also have a lower-durometer “sweet spot” (50) than TPEs (70). For optimum sealing, however, 30-durometer silicone is a good choice.
For designers of baby and childcare products, choosing an elastomer with the right durometer is critical. Teething rings that are too hard can hurt an infant’s mouth, but a grip toy that’s too soft won’t help a baby to build dexterity. For products that require a super-soft elastomer, gel-like silicones on the Shore 00 Hardness Scale have low levels of surface bleed, the release of oil from the surface of cured rubber. Super-soft TPEs are available, too, but these materials have higher levels of surface bleed.
What are the different material processing methods for silicones vs TPEs?
Silicones and TPEs also differ in terms of material processing. Both materials support injection molding, but silicones cannot be melted and reprocessed once molding is complete. By contrast, TPEs can be re-melted and re-molded multiple times. If sustainability is part of your value proposition, or if you may need to re-work manufactured products, TPE is probably a better choice. TPEs also take less time and energy to mold. They’re easier to work with in overmolding applications, too.
Overmolding, the process of creating a single part from two different materials, is used in infant care products like baby spoons. With overmolding, a rigid inner structure is covered by a softer material. TPEs bond not just to other TPEs, but to most common plastics. By contrast, silicones only bond readily to silicones. Plus, bonding silicone to plastic with low heat resistance can be especially challenging since silicone injection molding requires higher temperatures.
How do you choose a baby product manufacturer?
When seeking the ideal manufacturer for your product, focusing on a proven history of crafting high-quality baby products is essential. If you're considering different suppliers, it's worth investigating whether they have experience in manufacturing medical items as well. Suppliers with a background in the medical component and device field often adhere to precise processes due to the rigorous standards of the medical industry. This attention to detail often results in products that exceed expectations. At Extreme Molding, we have an extensive history of producing both medical and infant products.
Before choosing an elastomer for infant care products, designers need to consider all of their application requirements. Material properties and material processing are important but don’t forget about market acceptability. Extreme Molding can help you to determine whether silicone or TPE is the right choice for your products. If you're seeking a baby product manufacturer in the USA, reach out to us for a complimentary consultation.
Contact us to learn more.