When it comes to manufacturing high-quality products, understanding the differences between compression molding and injection molding is essential. These processes are widely used in industries like medical devices, baby products, kitchenware, and more. This post will provide a detailed comparison to help you determine which method best suits your product needs, with a focus on industries Extreme Molding serves.
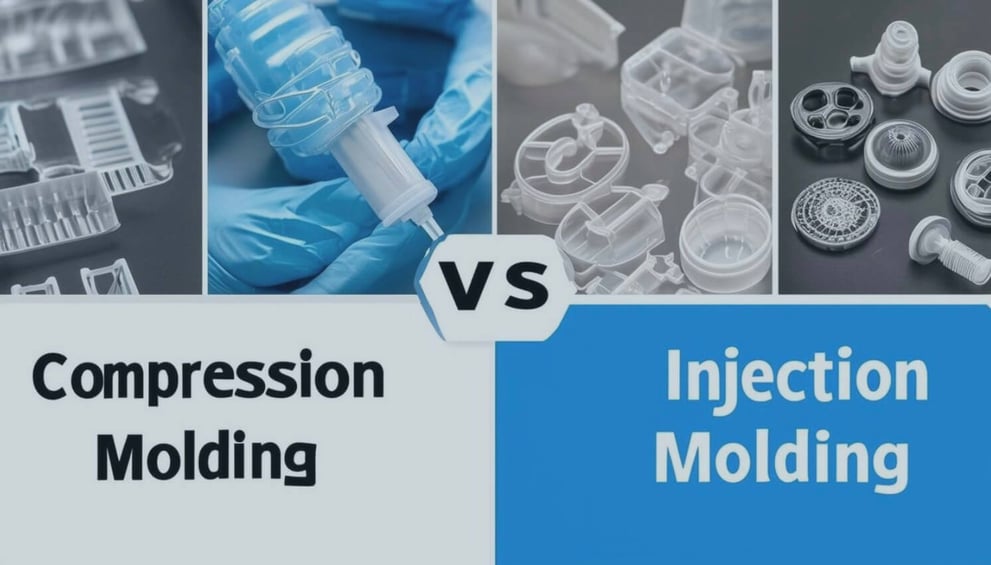
What is Compression Molding and What are the Common Applications?
Compression molding involves placing a pre-measured amount of material into a mold cavity. The mold is then closed and pressure is applied, causing the material to conform to the shape of the cavity as heat is introduced. Once cured, the material retains the shape of the mold.
Common Applications
- Medical Accessories: Compression molding is often used to create durable, flexible products like medical-grade liquid silicone components.
- Household products: Kitchenware such as utensils benefit from the uniform consistency provided by compression molding.
- Automotive parts: Car parts and automotive components benefit from compression molding due to its ability to produce high-strength, precise, and consistent parts.
Advantages of Compression Molding
- Cost-Effective for Smaller Runs: Compression molding tends to be more economical when producing smaller quantities, making it ideal for customized or limited-edition items.
- Ideal for Complex Designs: The process can accommodate intricate shapes, which is beneficial for industries like medical accessories manufacturing.
- Excellent for Large Parts: Compression molding excels in creating larger silicone parts, such as baby product molds or kitchenware items.
Disadvantages of Compression Molding
- Longer Cycle Times: Compared to injection molding, compression molding has a slower production speed, which could increase lead times. Additionally, in between cure cycles, the mold has to be dropped to near room temperature so that there is not premature curing of the next cycle, thus increasing the cycle time even further.
- Limited Precision: For extremely detailed components, compression molding may not offer the same level of precision as injection molding.
What is Injection Molding and What are the Common Applications?
LSR Injection molding involves injecting liquid material into a mold cavity under high pressure. The material is injected into a preheated mold to allow the material to cure into the final product shape.
Common Applications
- Medical Accessories: This method is ideal for small, intricate medical devices that require consistent, high-quality output.
- Pet Products: Items like pet toys and accessories, made from durable silicone, are commonly produced using injection molding.
- Baby Products: Pacifiers and sippy tops can be safely molded using this process due to its reliability and durability.
Advantages of Injection Molding
- High Precision: Injection molding provides precise detailing, making it perfect for medical-grade liquid silicone products that require tight tolerances.
- Scalability: Once the mold is created, injection molding can produce large volumes quickly and consistently.
- Low Waste: The controlled material injection helps reduce waste, making the process cost-effective and environmentally friendly.
Disadvantages of Injection Molding
- Higher Initial Costs: Due to the complexity of mold creation, the upfront costs for injection molding are higher compared to compression molding.
- Best Suited for Large Runs: For smaller production volumes, injection molding may not be as economical.
Compression Molding vs. Injection Molding Cost Differences
Compression molding generally involves lower initial costs because the molds are simpler and less expensive to produce. However, injection molding becomes more cost-effective in the long run when producing large volumes due to faster cycle times and greater efficiency.
Compression Molding vs. Injection Molding Flexibility Differences
In terms of design flexibility, compression molding offers greater versatility for larger or complex designs, but injection molding provides more precise control over intricate parts, making it more suitable for high-precision applications, particularly in medical-grade products.
Both compression molding and injection molding have their advantages depending on the specific needs of the industry. For smaller, complex designs, compression molding may be the best choice. However, if you're looking to scale up production with high precision and efficiency, injection molding might be the better option. Whichever method you choose, Extreme Molding offers the expertise and advanced technology to ensure that your product is manufactured to the highest standard.
Contact us today to discuss how we can help you create a product that meets your exact specifications and exceeds industry standards.